Observation of Single Pulse Discharge Phenomena
The mechanism of electrical discharge scar formation and debris removal in EDM are gradually being elucidated. However, there are still many unknowns regarding the discharge scar formation mechanism. In this study, gap phenomena caused by single pulse discharges with pulse widths of several hundreds μs were observed by using a high speed camera. Two high speed Microscopes were used for the observation. One highspeed Microscope was used to observe the EDM arc phenomena. The other microscope was used to observe the scattering phenomena of machining debris.Observation of arc phenomena.
Scattering phenomena of machining debris.
Discharge duration time 200 μs.
Small Hole Drilling EDM (Electrical Discharge Machining)
Small hole Electrical Discharge Machining is a drilling process of small holes with micro-diameters using the electrical discharge methode. The definition of small holes here are drilled holes with a diameter of 3 mm or less.
The micro electrical discharge machining is a drilling process of micro diameters utilizing the electrical discharge method. It is possible to process hardened steels, cemented carbides with high hardness (which are difficult to drill), and difficult-to-cut materials (tungsten, titanium, molybdenum, etc.) with high precision. Further, since EDM is performed while melting the material to be machined, the generation of burrs compared to cutting etc. is small, and high precision machining can be realized easily. The smale hole EDM machine is equipped with a dedicated power source capable of generating minute pulse energy unlike general electrical discharge machines. Using a pipe electrode thinner than the required hole diameter (considering the discharge gap), the liquid dielectric is discharged from the pipe to realize thin and deep hole processing. However, since a commercially available pipe electrodes are up to about 0.1 mm in diameter, it is necessary to use a rod (solid) electrode for small holes of 0.1 mm or less in diameter.
Also, in order to rotate the electrode, it is important to suppress the eccentricity and vibration of the shaft. Furthermore, in order to realize small hole electrical discharge machining, it is required to miniaturize the discharge pulse energy is required. In addition, since it is necessary to prepare a highly accurate micro diameter electrode, the “wire electrode discharge grinding method” (WEDG method) is used to form the electrode, using a wire moving along a guide to which the electric discharge machining method is applied. Electrode forming methods are widely studied.
Shaft forming by scanning electric discharge machining has been studied, and thin and long shafts can be formed in a short time and with high precision. Fig. 1 shows an SEM image of a shaft formed by scanning EDM. Fig. 2 shows an SEM image of a discharged machined micro hole (diameter of 10 μm) using a micro pin formed by the scanning EDM method.
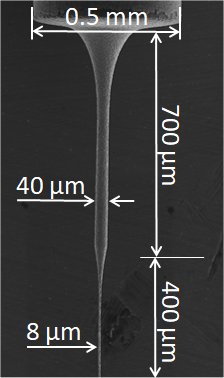
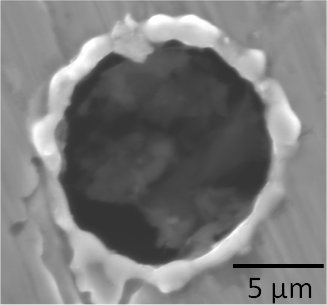